Barn raising: Ann Arbor architect Charles Bultman turns aging barns into beautiful homes
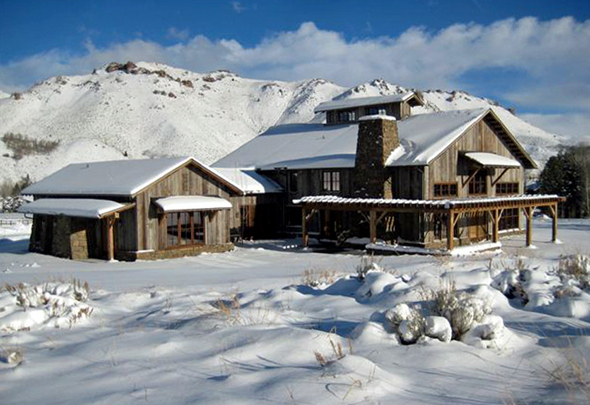
A barn home designed by Ann Arbor architect Charles Bultman.
Photo courtesy of Charles Bultman
He’s built sprawling chalets in Sun Valley and Nantucket-inspired homes in Virginia using the rough-hewn posts and beams of old barns as the skeleton and sometimes other barn wood (Bultman calls them barn parts) for floors, exteriors or inside trim.
While many of what Bultman calls “barn homes” come with the rustic feel of worn wood with a patina of time, he’s incorporated many styles into his designs.
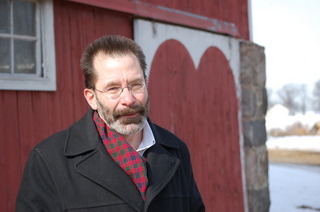
Ann Arbor architect Charles Bultman has worked on nearly 20 barn projects in the past dozen years across the country, but none of them in Washtenaw County.
Janet Miller | For AnnArbor.com
What they do have in common is warmth: Interiors rich with worn wood that come with texture and a history.
“They make a really warm and inviting interior. They have history, they have a story to them,” Bultman said. “At the same time, it preserves a barn.”
What they don’t do is stay on the original site. The frames are disassembled, cleaned and sometimes shipped across country where they are reassembled (usually by the same craftsperson who took it down) and used as a frame for a new structure. He only uses barns that are going to be razed.
While Bultman is a full-service architect, focusing on residential and small commercial projects, about half of his practice is with barns.
His first barn house was in 1999 in Sun Valley. He was working for an Ann Arbor firm at the time that had some experience in barn houses, and Bultman helped design a 13,000-square-foot chalet that incorporated five historic barns into the design.
He was hooked. Twelve years later, Bultman has worked on nearly 20 barn projects, mostly houses but also a commercial nursery and what he calls a party barn. His barn houses are located from Arizona to New Hampshire, with many of them concentrated in barn-loving New England.
“You get a kind of warmth and history and quality you don’t get with a drywall house,” Bultman said. “You can use new (wood), which means it’s bright. With barn wood, the colors are muted. You can get it with new materials, but it’s a 100-year process.”
Many barns have become obsolete, either in the way of development or too small for today’s large farm equipment and limping into disrepair.
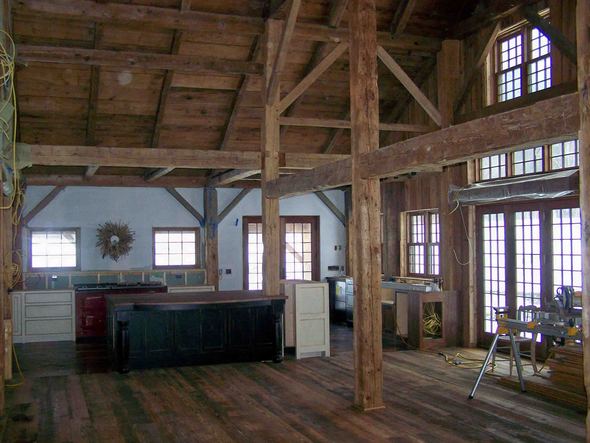
The interior of a barn home that Ann Arbor architect Charles Bultman designed in Vermont.
Photo courtesy of Charles Bultman
Sometime landowners ask a relatively small fee for the barn frame, Bultman said. Sometimes they just want the structure removed. But the real expense is in taking the barn down, cleaning it and reassembling it at a new location.
While he doesn’t usually scout for the barn frames himself -- that’s a huge time-eater -- there’s a network of people who do. They play matchmaker, connecting people looking for a barn frame with landowners interesting in removing a barn.
“Finding a barn is a lot like adopting a child,” he said. “Everyone knows where their barn comes from,” he said.
Barns were made from trees that grew closest to the farm: That means hardwoods such as oak, chestnut and walnut in the Midwest along with some softer woods such as pine.
New England barns were usually constructed from pine, spruce and hemlock. The posts are usually hewn, not sawed (the sawmill was too far to travel), giving them rich texture and a rustic look. And their sizes are not uniform, even within a single post or beam: It can measure 8 inches in one spot and nine inches farther up, Bultman said.
While his barn houses are usually open, airy and have lofted space, they can be rustic, quaint or even ultra-modern.
A relatively small barn house project on Madeline Island in Wisconsin includes a 30-foot by 40-foot barn, a small addition, a screened porch and a deck. There is no drywall inside the house. Instead, 10,000 square feet of barn wood was used to line the walls. For the floors, flooring from an pre-Civil War rendering plant in Missouri (think manure) was shipped to the site, cleaned, installed and further scuffed by construction workers to create a deeply rich surface, Bultman said.
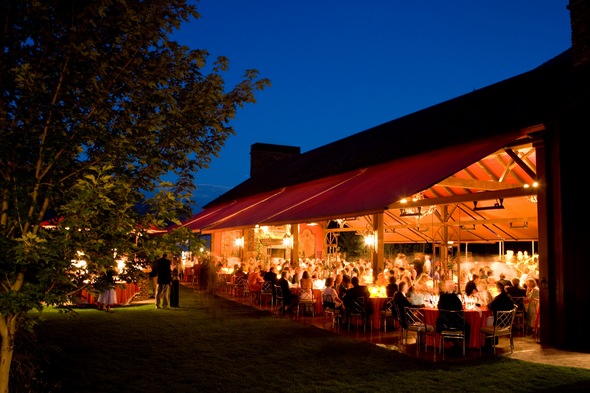
A party barn designed by Ann Arbor architect Charles Bultman.
Photo courtesy of Charles Bultman
“Barns were the industrial building of their day,” Bultman said. “They accommodate a huge range of styles.”
Barn houses tend not to be for the budget-minded. They tend to cost 50 percent more than traditional new housing, he said, and he hasn’t worked on one that has come in less than $1 million.
But there are ways to cut corners:
The customer who used the rendering plant floor ended up paying only $3 a foot to purchase, ship and clean the floor. A Pennsylvania customer he’s working with now is on the prowl for creative and inexpensive materials for a barn house.
While Bultman has never built a barn house in Washtenaw County, he’s designed them around the country, visiting on-site as needed. Having an architect live a distance from the project is old-school, he said. Think of Frank Lloyd Wright, the country’s most famous architect who was based in Chicago but who had projects from coast to coast.
Comments
Wolf's Bane
Thu, Feb 24, 2011 : 2 p.m.
Reuse and recycle! Great story!
Rebecca
Thu, Feb 24, 2011 : 1:31 p.m.
Is this the man who designed the barn on (I think) Joy rd? I'm in awe every time I drive past it.